Lapmaster Single Sided Lapping Machines
Lapmaster's lapping machine systems, when used with conventional abrasive, diamond superabrasive, or polishing media, can remove stock and finish virtually any solid material to your required specifications.
Our machines are engineered to lap surfaces so flat you can measure them in lightbands. . . surfaces so smooth, it is possible to get leak- proof mating without gasketing. Lapmaster's lapping and polishing machines provide the proper balance between rate of stock removal, finishing and flatness.
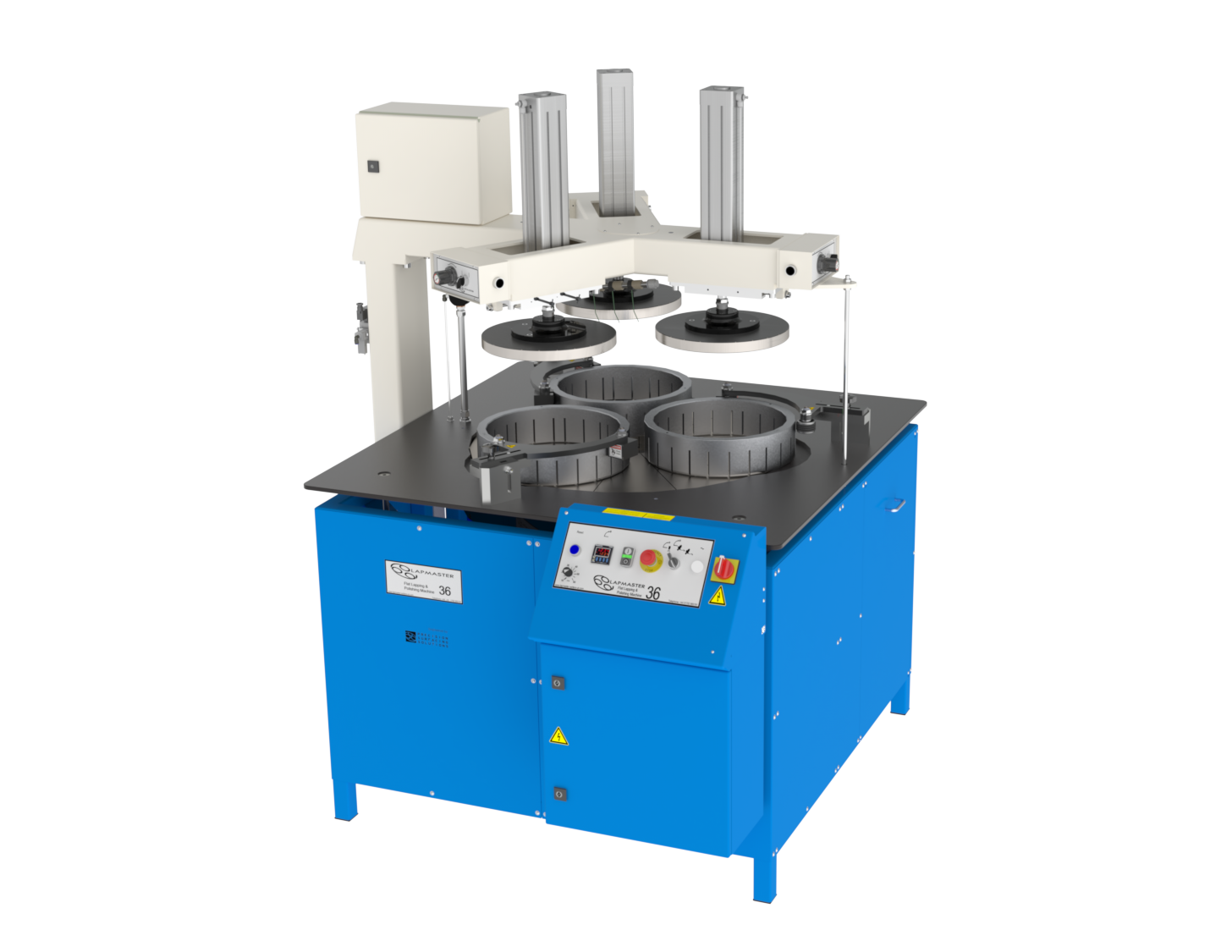
What sets LAPMASTER lapping machines and Polishing machinery apart from the competition is our versatility. Every machine is designed specifically for our customer's application. LAPMASTER has no predisposed tendency to promote one specific abrasive technology. The result is the development of the optimum process for the application. Conventional abrasive, diamond superabrasive, or lapping media. No matter what the application calls for, you can be sure that LAPMASTER will provide you with the best possible equipment and process to produce flat surfaces and extremely fine surface finishes with unfailing uniformity.
Fundamental Lapping Theory
The basic theory of lapping starts with the components being placed within the confines of conditioning rings directly onto the surface of a rotating lap plate that is coated with a precision film layer of slurry. The components should never come into direct contact with the lap plate surface. Through powered lap plate rotation, the loose and rolling abrasive particles within the slurry layer transfer cutting energy with their sharp cutting edges by penetrating the contact surface of the components removing microscopic chips of material. Concurrently the abrasive is acting on the lap plate via the contact surface of both the components and conditioning rings causing wear that when controlled by adjustable radial ring position will effect spherical curvature changes to maintain a flat lap plate condition.
Lapping successfully: Factors to consider
- Type of material being processed
- Speed of plate
- Pressure on work-piece
- Plate material
- Size and type of abrasive
- Vehicle used
- Flatness of plate
- Feed system
- Method of charging and conditioning the plate
- Plate temperature