Optical Pitch Polishing Machines
Air Bearing Optical Polishers
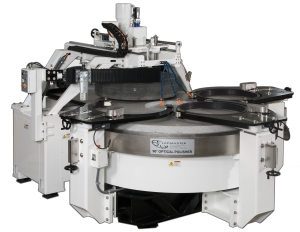
The air bearing line of optical polishers, available with 36" and 48" diameter, are designed so that the pitch lap and support plate ride on a very thin cushion of compressed air. These machines are driven from an electric motor via a lay shaft, and power is transferred to the lap using a multi-vee drive belt around the circumference of the support plate. This unique design virtually eliminates vibration at the polishing surface, and dramatically improves component flatness and finish results.
Conventional Optical Pitch Polishers
The conventional belt-driven line of optical pitch polishers, available with pitch laps from 60" up to 168" in diameter, are built on heavy-duty fabricated steel and cast iron machine bases. The design is intended to avoid the limiting problems that affect the production of very flat optics, especially vibration and thermal expansion.
The support plate is designed to produce an extremely stable, flat surface. It is made from solid granite, and is usually one-sixth as thick as it is wide to limit deflection under load. Granite is commonly used in flat pitch polishing applications for its slow rate of dimensional change in response to a change in temperature, and eliminates the need for water-cooling typically required on cast iron plate machines.
The support plate is mounted on a fabricated reinforced tripod shaped base with vibration dampening supports. The base is supported on three wedge isolator type, manually adjusted leveling feet. These feet are located at each leg of the tripod, providing maximum machine support and adjustment ability in the event of minor floor settlement.
The area surrounding the base is open for superior heat dissipation, and the motor and gear reducer are mounted to the side to prevent generating and trapping heat under the plate. This design gives the operator a shorter reach to the plate and easy access underneath the machine for maintenance.
The plate is mounted on the base with a turntable bearing that is approximately seventy percent of the plate diameter. This bearing design gives support under the centerline of the plate to balance the load and further limit deflection. The bearing is sized to handle axial loads many times greater than those expected during polishing for a long, trouble free life.
The outer race of the bearing has been modified to act as the driven pulley for the belt drive. This feature has the added benefit of placing the radial load at the centerline of the bearing to eliminate any overturning moment so as to further lengthen the service life. The fiber-reinforced v-flat belt used provides some elasticity to dampen any possible vibration in the drive train.
All of these measures to reduce vibration, thermal expansion, and deflection are aimed at maintaining a flat, stable and smooth running plate that will produce very flat parts as quickly and easily as possible.
Standard Features
- Heavy-duty fabricated steel and cast iron machine bases
- Rigid granite support plates with 6:1 or better aspect ratios to minimize deflection
- Granite Conditioners
- Positive drive workholder rings, conditioner, and pitch lap with VSD
- Adjustable, dove-tail slide pitch trimming bars for maximum accuracy and repeatability
- Suspended, non-contacting workholder rings
Standard Tooling
- Three high density cast anodized aluminum workholder rings
- Three phenolic workholder discs
- Operating and maintenance manual
Available Options
- Stainless steel slurry trough
- Recirculating slurry system
- Eccentric, oscillation of workholder rings
- Temperature control for slurry system